Events
Optical Interference Coatings (OIC)
16 June 2013 – 21 June 2013 OSA Virtual Event

The world's premier meeting for the global technical interchange in the field of optical interference coatings.
This meeting serves as a focal point for global technical interchange in the field of optical interference coatings. It will include papers on the latest results in research, development and the application of optical coatings. The general areas to be reported on include technologies used in deposition and process control, advances in materials as well as the properties of the various materials used as substrates and as coatings, the latest techniques used for the characterization of optical coatings, advances in computer and analytical design techniques, and the application of optical coatings for solar energy, lighting, display, nano-structures, biological, decorative, laser, lithography, and astronomical applications to mention a few uses.
The conference, like its predecessors, meets every three years and represents an important forum in which the latest advancements in the broad area of optical coatings from research to applications are reported. The format of the meeting includes invited papers by leaders in the field, oral presentations and poster sessions with ample discussion periods. There are no parallel sessions.
Invited Speakers
- Andreas Beutler , Mahr GmbH , Germany , Referencing and Form Measurements of Freeform Optics Invited
- Glen Cole , Thirty Meter Telescope , United States , Optical Fabrication and Metrology for the Thirty Meter Telescope Primary Mirror Segments Invited
- Turan Erdogan , Plymouth Grating Laboratory, Inc. , United States , Manufacturing Large-format Spherical and Cylindrical Laser Focusing Gratings using Scanning-beam Interference Lithography Invited
- Oliver Faehnle , FISBA AG , Switzerland , Machine Acceleration Effects on Computer Controlled Polishing Invited
- James Fienup , University of Rochester , United States , Phase Retrieval for Optical Metrology: Past, Present and Future Invited
- Mohammadreza Khorasaninejad , Harvard University , United States , Optics with Metasurfaces: Beyond Refractive and Diffractive Optics Invited
- Manyalibo Matthews , Lawrence Livermore National Laboratory , United States , IR Laser Processing Techniques for NIF Optics Invited
- Cormic Merle , United States , Metrology for the LSST M2: Large Holographic Stitching Technique Invited
- Brigid Mullany , Univ of North Carolina at Charlotte , United States , Fiber Based Polishing Tools for Optical Applications Invited
- Mahito Negishi , Canon Inc , Japan , New Stitching Algorithm using an Approximated Reference Shape Invited
- Joseph Owen , Univ of North Carolina at Charlotte , Diamond Milling of IR Materials Invited
- Jyrki Saarinen , University of Eastern Finland , Finland , Additive Manufacturing for Small and Medium Sized Optics Invited
- John Schaefer , Raytheon EO Innovations , United States , Advances in Diamond Turning Invited
- Sven Schröder , Fraunhofer IOF , Germany , Surface Characterization of High-End Optical Components using Light Scattering Invited
- Robert Smythe , Apre Instruments , United States , Interferometric Measurement of Mid-Spatial Frequency Wavefront Errors Invited
- Simon Thiele , University of Stuttgart, ITO , Germany , Complex Micro-optics by Femtosecond Direct Laser Writing Invited
- Jurgen Van Erps , Vrije Universiteit Brussel , Belgium , Prototyping and Replication of Polymer Freeform Optical Components Invited
- Reinhard Voelkel , SUSS MicroOptics SA , Switzerland , Novel Fabrication and Testing Methods for Micro Optics Invited
- Christian Weingarten , Fraunhofer ILT , Combination of Laser-based Process Steps for Optics Manufacturing Invited
- Richard Youngworth , Riyo LLC , United States , Adopting and Using Optical Standards Invited
Plenary Speakers
Patrick McCarthy
Giant Magellan Telescope, USA
Giant Magellan Telescope, Optics and Science
The world’s next great astronomical observatory – The Giant Magellan Telescope – will be used to explore the early Universe and to search for life on other planets. I will describe the scientific mission and the engineering challenges involved in its design and construction.
Bio: Patrick McCarthy is the Interim President of the Giant Magellan Telescope Project. He received his Ph. D., in Astronomy from U. C. Berkeley in 1988. He went to the Carnegie Observatories first as a Carnegie Fellow and then as a Hubble Fellow in 1991. In 1993 he joined the scientific staff at Carnegie. He is known for his work on galaxies in the distant universe and, in particular, for his study of distant low frequency cosmic radio sources: sign posts to massive galaxies undergoing rapid accretion on to super massive black holes. In the late 1990s, McCarthy and his colleagues identified a new population of galaxies with colors indicative of very early star formation. Study of these faint red galaxies is now one of the most active areas of research in astrophysics.
McCarthy has been active in scientific and management oversight of large science projects and organizations. He has chaired numerous panels for NASA and the NSF providing independent oversight of the Hubble Space, Spitzer Space Telescope, and large telescopes on the ground. McCarthy led the Giant Magellan Telescope (GMT) Science Working Group that wrote the scientific case for the telescope project and defined the scientific and technical requirements for the facility.
Today, he leads the team of scientists and engineers building the Giant Magellan Telescope (GMT), an enormous instrument comprised of seven primary mirror segments—the seven largest mirrors ever made—that will stretch to more than 80 feet across once complete. The GMT will explore the cosmos to observe the first stars in the universe, offering images 10 times sharper than those coming from the Hubble Space Telescope. Since 2008, he has served as the head of the non-profit corporation, GMTO, that is charged with carrying out the development, construction and operation of the telescope and related facilities. My day-to-day responsibilities include ensuring that the telescope and its instruments will be able to address the key questions at the forefront of astrophysics in 2020 and beyond.
Joshua Smith
California State University Fullerton, USA
Using Optics and Precision Metrology in to Measure Black Hole Mergers from Across the Universe with LIGO
On September 14, 2015 the two detectors of the Laser Interferometer Gravitational Wave Observatory (LIGO) detected gravitational waves from the merger of a binary system of black holes. This discovery could not have been made without a century of advances in optical technology and precision metrology. I will give an overview of gravitational waves detected by LIGO to date and describe the optics involved and current optical challenges. I will end with prospects for future gravitational-wave observations made with even more advanced optics.
Bio: Joshua Smith directs the Gravitational-Wave Physics and Astronomy Center (GWPAC) and is an associate professor of physics at California State University, Fullerton. Currently he is active in gravitational research, astronomy education research, and teaching physics and astronomy. His research is focused on detecting gravitational waves from astronomical sources using the Laser Interferometer Gravitational-wave Observatory (LIGO) in collaboration with colleagues in GWPAC and in the international LIGO Scientific Collaboration.
Jannick Rolland
University of Rochester, USA
Freeform Optics from Design to Manufacture and its Envisioned Impact on Technology to Enable the Science of Tomorrow
All-reflective optical solutions have long hold their place in optical system design from small scale optics as in microscopes to large scale optics as in telescopes. Yet reflective solutions have suffered from obscuration or the need to restrain surfaces to be off-axis conics or aspherics. The ability to recently fabricate freeform surfaces opens up new spaces for optical design, driven by applications spanning demands in mobility, larger fields of view, apertures, light weight and compactness. I will present success stories designing and prototyping designs with freeform surfaces and highlight pathways and challenges associated with their emergence.
Bio: Jannick Rolland is the Brian J. Thompson Professor of Optical Engineering at the University of Rochester and she directs the NSF I/UCRC Center for Freeform Optics (CeFO).
Rolland joined the University of Rochester in 2009 after advancing her career from Assistant to Full Professor at CREOL, the College of Optics and Photonics at the University of Central Florida. Together with colleagues at the University of Rochester and partners at the University of North Carolina at Charlotte, she launched in 2013 the Center for Freeform Optics (CeFO) as an international consortium aimed at advancing the science and engineering of freeform optics. Rolland earned an optical engineering diploma from the Institut D'Optique Théorique et Appliquée, France, and a PhD in Optical Science from the College of Optical Sciences at the University of Arizona. She is a Fellow of OSA, SPIE, and NYSTAR. She is the recipient of the 2014 OSA David Richardson Medal. She is known for her innovations since the 90s in head-worn displays, and more recently her innovations in 3D microscopy and telescope designs.
Sponsors
Cooperating Societies:
The European Optical Society
Corporate Sponsors:
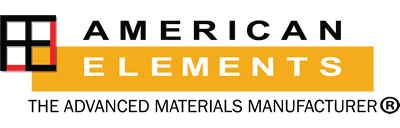

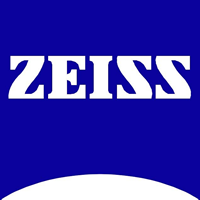
Corporate Contributors:
Evaporated CoatingsFISBA Optik
Iridian Spectral Technologies
Materion
Shincron
Exhibitors:
Agilent Technologies
Dynavac
Evatech
FTG Software
JA Woolam
Kaufman & Robinson
Leybold Optic
Optical Reference Laboratory LLC
Optics Balzers
Optilayer
Perkin Elmer
Poggisoft
Tecport Optics
Telemark
Thin Film Center
Umicore Thin Film Products
Vacuum Process Technology